SYENMAINT PROJECT
POR CAMPANIA FESR 2014 – 2020 Priority Axis 1 “Research and Innovation” Specific Objective 1.1 Increase in the innovation activity of enterprises Action 1.1.2 – Support for the purchase of services for technological, strategic, organizational and commercial innovation of enterprises Action 1.1.4 – Support for collaborative R&D activities for the development of new sustainable technologies, new products and services. Public notice for support to Campania companies in carrying out feasibility studies (Phase 1) consistent with RIS3.
Project description
SYENMAINT® PLATFORM is an integrated platform for Industry 4.0, able to carry out continuous and automated monitoring of production assets, according to a vertical, modular, scalable and multilayer architecture, for the innovative management of maintenance and the entire life cycle of plants and production infrastructures, through a system composed of: sensors, hardware, firmware and software. It constantly monitors production phases, machines and infrastructures, quality of production results, stocks, personnel, costs, by the use of intelligent and interconnected IIoT sensors, for the management of predictive diagnostics, optimized management tools of operating costs, integration and / or interfacing of production software systems.
Objectives
The objective of the SYENMAINT project is to prepare, through the following activities:
- Economic-Financial Feasibility Analysis
- Technical Feasibility Analysis
- Definition of Functional and System Architecture
- Specification Requirements
- Preliminary prototype implementation
- Functional test execution
the industrialization and marketing of the proprietary system “SYENMAINT® PLATFORM”, to be used for predictive management of the maintenance of production assets, based on the dynamic scheduling of interventions, to reduce operating costs, improve quality and safety, thanks to monitoring constant and automated.
Results
Based on the activities carried out as part of the SYENMAINT Project, and on the basis of all the project deliverables that have been produced, the SYENMAINT Platform product was also developed within the company and in prototype form. This solution which in a preliminary form implements what is already provided for in the technical project documentation, which has been developed and produced, within which the technological choices to be used have been elaborated, with respect to the state of the technological art analyzed.
Project co-financed by the European Regional Development Fund

SIADIAG TROLLEYS PROJECT
Call POR CAMPANIA FESR 2014 – 2020. Priority Axis 1 “Research and Innovation”. Specific Objective 1.1 Increase in the innovation activity of companies. Action 1.1.2 – Support for the purchase of services for technological, strategic, organizational and commercial innovation of companies. Action 1.1.4 – Support for collaborative R&D activities for the development of new sustainable technologies, new products and services DGR n. 65/2017. Public notice for support to Campania companies in the implementation of technology transfer projects (Phase 2) consistent with RIS3.
Project description
Innovative self-powered system for diagnostics of carriages for railway maintenance. The objective of the SIADiagCarrelli project is the development of a diagnostic system for railway carriages based on sensors powered by an innovative self-supplying component capable of recovering energy from the vibrational dynamics of current air shock absorbers, by means of a piezoelectric membrane. The trolley diagnostics concerns the acquisition of physical quantities from the synchronization and processing of which, through algorithms object of the research and innovation activity of the project, it will be possible to identify the intrinsic anomaly conditions of the trolleys and of the case-trolley couplings, and trolley- rail, in a “direct” manner and, possibly, the anomalies of the railway infrastructure relative to the road site, in an “indirect” manner. Project co-financed by the European Regional Development Fund.
Results
SYENMAINT contribution. SYENMAINT®, as an innovative startup, has brought, within the SIADiagCarrelli project, all the experience of its founders and collaborators, in the design of innovative monitoring, diagnostics and maintenance systems and all its skills in in the field of railway diagnostics, from intelligent sensors to fw / sw correlation algorithms between monitored physical quantities and anomalies to be detected also through the strong capabilities of design, development and electrical, electronic and mechanical integration. SYENMAINT® has the honor of fulfilling the role of scientific coordinator of the project. In detail, SYENMANT® took care of the acquisition and synchronization of information from the various sensors that carry out all the useful monitoring (even structurally in an indirect way), of the definition and development of the information processing algorithms in order to correlate the data acquired under the structural anomaly conditions of the bogies, of the shock absorbers, in particular the primary and secondary air shock absorbers, and of the other bogie-rail and body-bogie couplings. Furthermore, he oversaw the implementation of the information management logic / policy and their transmission to a central unit on board the trolley, where it is possible to store / view / analyze, through User interfaces, all the acquired information, the most significant data collected for the management of anomalies and the corresponding maintenance interventions, correlated to the anomalies detected. SYENMAINT® also carried out the electrical and mechanical design and followed the installation and physical integration of the sensors and the vehicle dynamics monitoring and diagnostics system. He then carried out all the pre and post installation laboratory test management activities, all activities related to the testing of the measurement system and its certification.
Contribution from the Industrial Engineering Department of the University of Naples “Federico II”. The innovative idea (patented) on which the SIADiagCarrelli project is focused consists of an air spring (also called air spring / pneumatic spring) which integrates an energy recovery system inside. Through this system it is possible to power a sensors placed on the trolley, functional for monitoring and diagnostic purposes, without resorting to the usual on-board wiring, which is expensive from the point of view of installation and maintenance. In this way the trolley system becomes energetically autonomous and independent from the surrounding systems. The prototype created within the SIADiagCarrelli project saw the unit of the Department of Industrial Engineering of the University of Naples “Federico II” (DII-UNINA) actively involved in the design and development of air suspension prototypes with of energy recovery. The DII-UNINA unit also carried out the design and development of the energy storage system, necessary to power the network of sensors for monitoring and diagnostics of the truck. With particular reference to trolley diagnostics, the DII-UNINA unit contributed to the development of a self-diagnostic system for the air spring and the accumulation system.
CNR-ISASI contribution (formerly IMM). The aim of the SIADiagCarrelli project is to develop a diagnostic system for railway bogies based on sensors capable of detecting physical quantities such as acceleration, vibrations etc. The electricity required for the operation of these sensors is guaranteed through the development of innovative systems capable of recovering energy from the vibrational dynamics of the trolleys themselves. In this context, the activity of the Naples section of ISASI (formerly IMM) is focused on the study and choice of physical sensors suitable for the measurement of the physical quantities in question and the definition of the most suitable configurations for the integration of the sensors themselves in the measurement and generation of electricity. This activity, in a preliminary phase, required a careful evaluation of the state of the art, aiming to identify the types of hardware components for sensorization (accelerometry, inclinometry, gyroscopy, inertial, strain gauge) of the railway trolley in the most appropriate way for the purpose. to satisfy the required functional design requirements. In particular, the analysis was aimed at the measurements of accelerations along the three axes (longitudinal, lateral and vertical) and the yaw rate. For the various measures to be carried out, the fundamental parameters and the main specifications to be respected for use in the railway sector have been defined. In particular, the following parameters have been identified as fundamental: Full scale, Frequency response, Sensitivity, Temperature range, Shock resistance, Electricity consumption. The physical principles of the main types of sensors available were evaluated, comparing their performance. And the possible implementation and design of a communication platform was envisaged, necessary for the integration of the various sensors with the aim of obtaining a homogeneous data flow that can be easily interpreted and / or transmitted. To minimize the number of interconnections to be made with the external board for data transfer, a two-wire connection based on an I2C type serial protocol was chosen. In particular, there are the following two serial communication lines: SDA (Serial DAta) for data; SCL (Serial CLock) for the clock. All the circuitry has been developed and programmed to minimize power consumption and thus make the system self-sufficient with the energy produced by the Energy Harvesting system. In relation to this last part of the activity, an in-depth analysis and configuration of the control logic of the sensor system was necessary. This activity made it possible to find the optimal balance between energy consumption and dynamic performance of the system; furthermore, the widest possible flexibility in the configuration was considered so as to be able to adapt, within certain limits, to the required operating parameters. In fact, different configurations were tested and developed according to performance and the relative electrical absorption was measured. The system prototype thus developed has a maximum absorption below 30mW with an operation frequency of about 250Hz, ie values that are fully compatible with the powers generated by the energy harvesting system and the observation of the trolley dynamics.
Monticelli Group contribution. Dynamic simulation of railway carriage driving. The SIADiagCarrelli project involves the installation, on a railway trolley, of piezoelectric elements inside the air springs (torpress) and of self-powered sensors which aim to acquire data and take into account the driving dynamics of the railway vehicle . By Running Dynamics we mean the set of acquisition parameters that represent: the effect of the response of the vehicle system to the stresses exerted, during the run, by the acceleration track in the bushing, carriage and body; Driving comfort, associated with mechanical vibrations resulting from track irregularities, functions of the Sperling Index and the value of vertical and transverse accelerations. Specifically, the MONTICELLI GROUP has created equipment to reproduce: pitching and rolling motion, loading the crate on the trolley, rotation of the wheelset. These equipment were used in order to validate / verify the correct functioning of the sensors installed on the trolleys. The trolley case simulation test is performed through a press, which allows you to apply the desired load on the air springs, and then evaluate their state through a pneumatic test bench. Rolling and pitching tests are performed by subjecting the trolley to an effort through hydraulic cylinders positioned in axis with the primary suspensions in order to obtain the desired inclinations. The rotation test was performed with the aid of electric motors coupled with interface elements to the carriage axles in order to obtain a smooth transmission of motion. Transmission shaft design: The acquisition of running data was also carried out with the preparation of 100m of track where the sensorized prototype trolley can be launched. In order to position the trolley on the tracks, a carousel will be used, this allows you to rotate a portion of the tracks. When the trolley is positioned on it, this rotates 90 ° returning in axis with the tracks, then allowing the trolley to move on them. Defects. As part of the SIADiag project, the Monticelli Group, through its corporate know-how, has analyzed all the maintenance interventions carried out, both cyclical and corrective maintenance, to extract an assessment of the defects found. The field of investigation covers all the maintenance interventions carried out in the last 5 years of activity, through events derived from experience, calculations and databases of the last five years of maintenance activities carried out by defining the percentages of defects detected on the components of the rolling stock caused by the driving dynamics of the railway vehicle and / or from manufacturing / aging errors of the same. With reference to the cyclical and corrective maintenance of the “TROLLEY” safety device, for reasons strictly related to the driving dynamics of the railway vehicle, the operations to be kept under observation are the following: Identified the processes involved and the defects found on the “trolley” component “, Tables and graphs have been drawn up with reference to the two classes of vehicles of our competence, where there is a higher percentage of maintenance defects generated by the driving dynamics for vehicles with speeds below 200 km / h compared to vehicles with speed greater than or equal to 200 km / h, a difference probably caused by the different conception of the railway network dedicated to HS. It can be observed that the main problems related to the driving dynamics (track layout, natural obstacles, trolley speed) are encountered for trolleys traveling at low speed, however, the problems deriving from manufacturing defects but above all due to the aging of the components. detect for high speed trolleys. This difference, even if minimal, is probably due to the different conception of the two lines AV and BV.
Project co-financed by the European Regional Development Fund
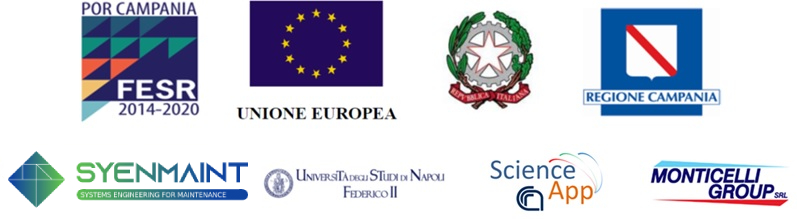